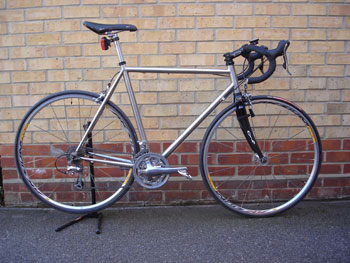
Introduction
Way back in 2006 I decided to design and build my own bike. The picture on the right is the finished article. I built the frame using (what was then) a brand new material from Reynolds, called Reynolds 953. This material is a high strength stainless steel specially developed for lightweight bike frames. All frame tubes and components (bottom bracket shell, dropouts, brake bridge etc) are Reynolds 953. The front forks are carbon fibre.
I was lucky enough to get material from the second production batch, so this was one of the first bikes to be built using the new material. As it happens, I don't believe that the material has taken off in quite the way that Reynolds had expected (they had predicted that this material would compete directly with carbon fibre). I have not seen many production 953 frames, probably due to the high material cost, and the difficulties in working with this material.
The decision to use Reynolds 953, rather than a more traditional (and easier to work) alternative such as Chromoly or even aluminium, was partly emotional (shiny new material), and practical in terms of the finish. Because the material is Stainless Steel there is no need to paint the frame, and it should look as good as new for years.
Reynolds 953 is a mar-aging stainless steel which can achieve a yield strength greater than 1500MPa, which is more than twice the yield strength of cold worked stress relieved 3-2.5 titanium. Because of its high strength, Reynolds have been able to produce tubes with material thicknesses down to 0.3mm, which obviously saves weight. The tubes and components are formed and heat treated by Reynolds which makes them harder to work, but saves having to age (heat treat) the frame after it has been welded. Other components have been purchased, such as a Shimano 105 groupset (10 speed), Carbon forks, Mavic wheels.
I have designed the frame myself using my own body dimensions to optimise the frame geometry. If I've done my sums right, then it should be a perfect fit for me. The frame has been designed as a road racing bike for a fat bloke whose welding is a bit suspect (hence the oversized tubes).
If you want to build your own bike frame, then you're going to need The Paterek Manual. Written by Tim Paterek, who appears to be the worlds authority on building bike frames in your own garage, has shared his expertise in this very detailed book. Tim is an old American guy whose been building frames all his life. I get the feeling he would not approve of my own project - he likes things done the old fashioned way (with old fashioned materials) and believe that people should learn to walk before they run.
I also subscribed to a couple of mailing lists which are an endless source of useful (and sometimes not so useful) information. I never needed to post any questions because there is so much information in the archives, and new information is always coming in.
As it happens, Tim was right: You should learn to walk before running a marathon. One week with a TIG welder is enough for me to decide to hand over to a professional. Kevin Winter of Winter Frames in County Durham took on the job, and I must say, finished it to the highest standards. As you would expect the thin material was very difficult to weld. I just had not realised how difficult it would be (although, I still tell myself it was the TIG welding machine that was the problem, and not the guy using it!).
The bike was finished in February 2007 (14 month project). The bike is great to ride, and looks the business too!